Disclosure
If you click to purchase a product or service based on our independent recommendations and impartial reviews, we may receive a commission. Learn more
Did you know that if you end up using a website builder that we recommend through our website, you help support this site? There are no extra costs to you at all and it allows us to continue to write helpful reviews to help you and others who are just starting to build websites.
We’ve always believed in transparency on the internet and so here’s how it works.
If you are only trying a website builder and signed up for its free program (no cost to you), we won’t earn any commissions because of that. It is only if you are happy with the website builder and decide to upgrade to their premium package, then the website builder will pay us a small referral commission later.
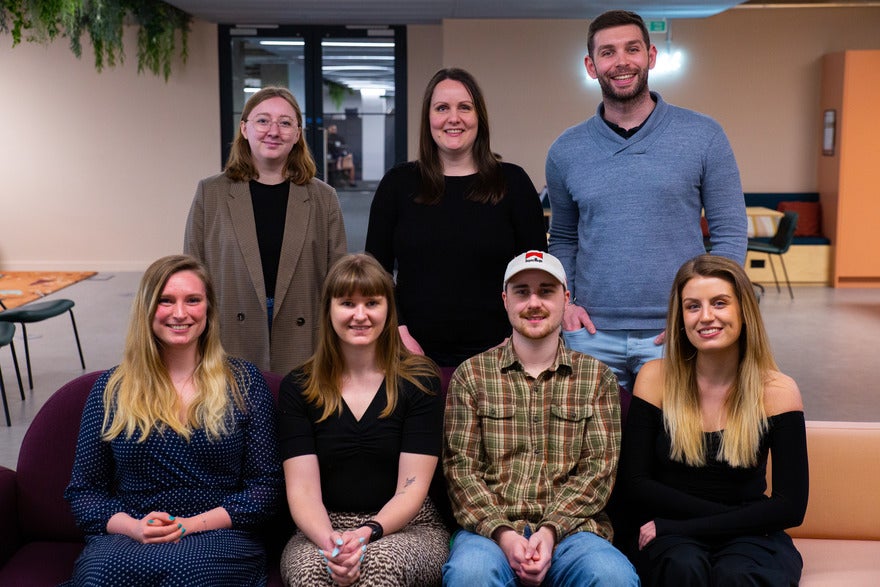
So the commissions (if earned) are paid from the website builders, not from you.
Our goal of this website is to help you become more informed, and help you save time by giving you as much helpful information about our experiences with website builders as possible.
There’s no need to repeat our trial-and-error mistakes by spending days and weeks testing out all the website builders available in the market, when you can read our website builder reviews and short-cut your way to testing only a couple.
The commissions that we receive will help us create more useful information, reviews, tips and tutorials to continue to help you. Not to mention you will earn +1,000 karma points! :) [Read about us and our journey here]
Please note that we have not been given any free products, services or anything else by these companies in exchange for mentioning them. We are very selective in who we review, and we are objective about our reviews listing out the goods and the bads based on our own experiences. Most of the website builders that we’ve reviewed are the ones that we’ve actually used in the past in building real websites, and we know them inside and out. We share the goods and the bads, and everything in between so we try not to be biased in anyway.
If you have any questions regarding the above, please do not hesitate to contact us (our email is below)
We genuinely hope we’ve been helpful and good luck in your website!
The WBE Team
Google Analytics & Privacy
This website uses Google Analytics, a web analytics service provided by Google, Inc. (“Google”). Google Analytics uses “cookies”, which are text files placed on your computer, to help the website and its partners analyze how users use the site, or show them relevant advertisements when they visit other sites across the Internet in the Google Display Network (This is often called ‘remarketing’). The information generated by the cookie about your use of the website (including your IP address) will be transmitted to and stored by Google on servers in the United States. Google will use this information for the purpose of evaluating your use of the website, compiling reports on website activity for website operators and providing other services relating to website activity and internet usage. Google may also transfer this information to third parties where required to do so by law, or where such third parties process the information on Google’s behalf. Google will not associate your IP address with any other data held by Google. You may refuse the use of cookies by selecting the appropriate settings on your browser, or you may be able to opt out of customized Google Display Network ads by visiting the Ads Preferences Manager (https://www.google.com/ads/preferences/), and the Google Analytics Opt-out Browser Add-on (https://www.google.com/settings/ads/plugin). By visiting this website, you consent to the processing of data about you by Google in the manner and for the purposes set out above.
10 comments