The 6 Best Blogging Platforms in 2024: Our Top Picks
If you click to purchase a product or service based on our independent recommendations and impartial reviews, we may receive a commission. Learn more
Blogs are the most common form of information transmission on the web due to their high accessibility and endless variety – from food to the history of art, there’s a blog for everything!
But with a website builder can you truly make a blog your own, since you can design it to suit your content, as well as market your site to wider audiences and monetize it. In fact, many website builders started as just blogging platforms, and over the years have added more and more features to keep bloggers happy.
Here, we’ve collected the top six blogging platforms in our research and organized them by blogging style. Which blogging platform is best for you will differ on what type of blog you intend to create, but from our research, we can confidently say that Wix is the best overall.
Our Top 6 Blogging Website Builders:
- Wix – Our top choice for blogging
- Squarespace – For art blogs
- WordPress.org – For news blogs
- WordPress.com – For affiliate blogs
- Hostinger – For simple blogs
- Webflow – For business advice blogs
Short on time? Find the best platform for your art with our 3-minute quiz.
Compare the 6 Best Blog Website Builders
Get a quick overview of our top six blogging platforms below. You can compare ratings, pricing, features, and more side-by-side to help you choose the best blog website builder for you.
BEST IN TEST ![]() | ![]() | ![]() | ![]() | ![]() | |
Wix | Squarespace | WordPress.org | WordPress.com | Hostinger | Webflow |
Overall Rating 4.9 | Overall Rating 4.8 | Overall Rating 4.1 | Overall Rating 4.1 | Overall Rating 3.5 | Overall Rating 3.5 |
Starting from | Starting from | Starting from $2.95 (for hosting) | Starting from $4 | Starting from
79% off in early Black Friday sale: $2.49 + 3 months free (for 48-months) | Starting from $14 |
Publish for free | Publish for free | Publish for free | Publish for free | Publish for free | Publish for free |
Storage space 2GB – Unlimited | Storage space Unlimited | Storage space 50GB – Unlimited | Storage space 3GB – 200GB | Storage space Unlimited | Storage space 1GB – 400GB |
Comments | Comments | Comments | Comments | Comments | Comments |
Search feature | Search feature | Search feature | Search feature | Search feature | Search feature |
Ease of use 4.4 | Ease of use 4.4 | Ease of use 3.2 | Ease of use 2.7 | Ease of use 3.9 | Ease of use 2.1 |
View Wix | View Squarespace | Visit WordPress | Visit WordPress | View Hostinger | Visit Webflow |
What Types of Blogs Are There?
There are as many blog types out there in the blogosphere as niche subjects. We could go through each one, but we think it is more productive to give you the three styles of blog every blog roughly falls under:
- Persuasive blogs – Blogs that aim to convince the reader to do something, whether buying a product or signing up for a newsletter. These blogs are frequently attached to an existing online store or business.
- Informational blogs – These blogs provide valuable information to readers. They have ads or affiliate links but the primary goal is to inform. They also may have multiple authors and upload frequently.
- Entertainment blogs – Blogs that want you to feel something, and are created simply for the enjoyment of the creator and audience. These types of blogs are done more as a hobby than a job, but can still be monetized.
Most website builders will have blogging features, but not all will give you the tools to manage them. Website builders like WordPress, for instance, let you filter through your lists of blogs, schedule them to go live at certain times, and put certain posts behind a paywall – whereas Hostinger just lets you write and post content. Depending on what type of blog you want to create, these tools will either be essential or a nice addition.
Best for Persuasive Blogging
Lifestyle blogs, online store blogs, affiliate blogs, influencer blogs, etc.
- Well-designed templates
- Advanced SEO settings
- Ecommerce
- Email marketing capabilities
- Google AdSense
- Minimum storage space – 5GB
Top Choice: Wix
Starting price: $17 per month
Read our full Wix Review
Wix
Our top choice for blogging
- Easy platform to use
- Publish on free plan
- Endless creative freedom
Free plan available
Paid Plans: $17 - $159 / month
Pros
-
Create a whole website including a blog
-
Beginner-friendly editor
-
Advanced SEO support
Cons
-
Can't switch template once site is live
-
Premium plans start at $17 per month
-
Lacks storage on cheap plans
If you are interested in generating revenue with your blog as soon as possible, then Wix is the builder you should be looking at. Integrations with ecommerce, newsletter marketing, and Google AdSense mean you can hit the ground running and monetize your blog as soon as possible.
Wix also stands out in our research for maintaining the tricky balance between offering professional blog management tools – like those found with WordPress.org – while still being easy to use. This makes it perfect for experts and beginners alike.
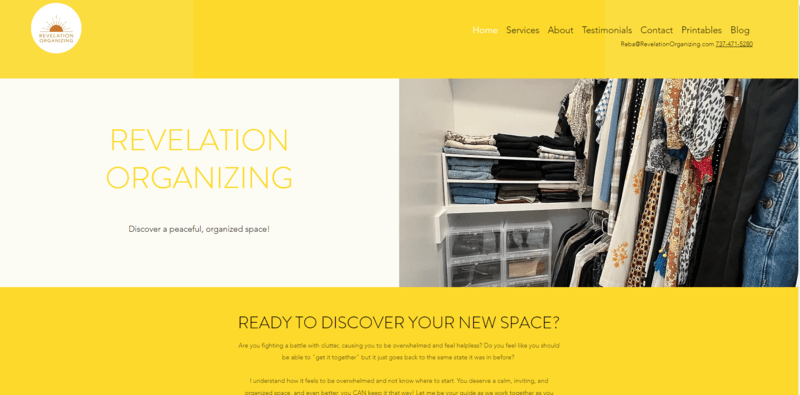
Wix is our top choice for blogging because of how versatile it is as a website builder. You get to choose an expertly designed blogging template from across several industries and then add any number of features you wish. You can simply add Wix Blogging to your site and you have your blog, shrinking many of the anxieties when you start a blog for the first time. You can also add Wix Stores for ecommerce capability. However you want your blog to look and function, Wix can accommodate it.
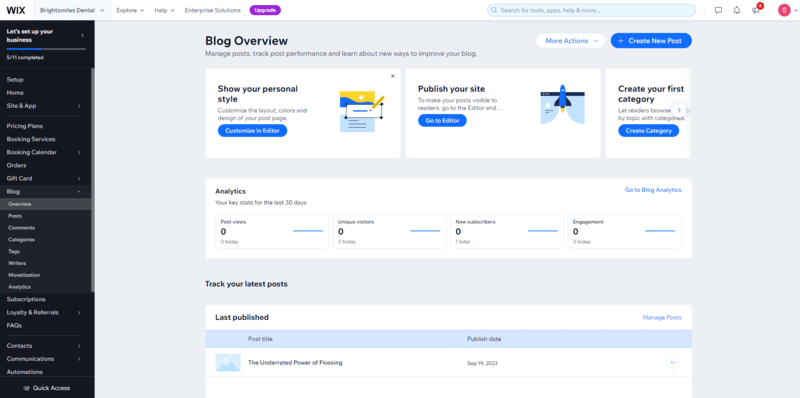
Wix’s blogging features have nothing to be shy about either. You get a vast variety of design options from fonts to background colors and even images and video. There’s also a handy sidebar in the backend editor that lets you adjust each Wix post’s SEO setting and whether you want to monetize it with a subscription plan. If you want to publish a lot of content quickly, then Wix’s AI Writer can help you create content at a much quicker pace. You can schedule up to 1,500 pieces of content on Wix’s cheapest plan for $17 per month (billed annually).
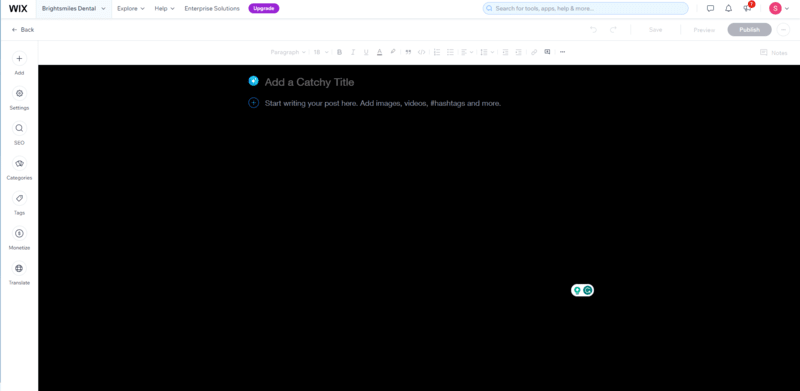
What’s the Best Value Plan?
Here’s a full list of the pricing for Wix’s website plans, all billed annually:
- Free: $0 per month
- Light: $17 per month
- Core: $29 per month (Basic ecommerce)
- Business: $36 per month (Standard ecommerce)
- Business Elite: $159 per month (Advanced ecommerce)
Wix’s free plan may seem like the go-to, but be warned you’ll have to contend with limited features, a Wix domain, and banner ads all over your site. The Light plan will get you everything you need for basic blogging, but its lack of ecommerce and small storage space (2GB) means it isn’t very scalable.
To get the full potential out of your blog, we recommend the basic ecommerce Core plan. With ecommerce included and 10 times the storage (20GB), it’s perfect for all your blog monetization goals. Plus, if you want to get 10% off your purchase at checkout, use our exclusive code TAKE10
More Information:
- See Wix’s potential for an online store with our Wix Ecommerce Review.
Alternative: WordPress.com – For affiliate blogs
Starting price: $4 per month
Read our full WordPress.com Review
WordPress.com
For affiliate blogs
- Built purely for blogging
- More advanced platform
- Coding skills are helpful
Free plan available
Paid Plans: $4 - $45 / month
Pros
-
Powerful built-in blogging tools
-
Easier version of the CMS WordPress.org
-
Cheapest starting price at $4/month
Cons
-
Not user-friendly for beginners
-
Not as powerful as WordPress.org
-
No autosave function in editor
WordPress.com is the easier-to-use, website builder version of the CMS WordPress.org. Whereas the latter has arguably the best blog management tools on the web, it is also not very beginner-friendly. WordPress.com bridges the gap and gives users advanced built-in blogging tools while also letting them use an accessible editor and design tools.
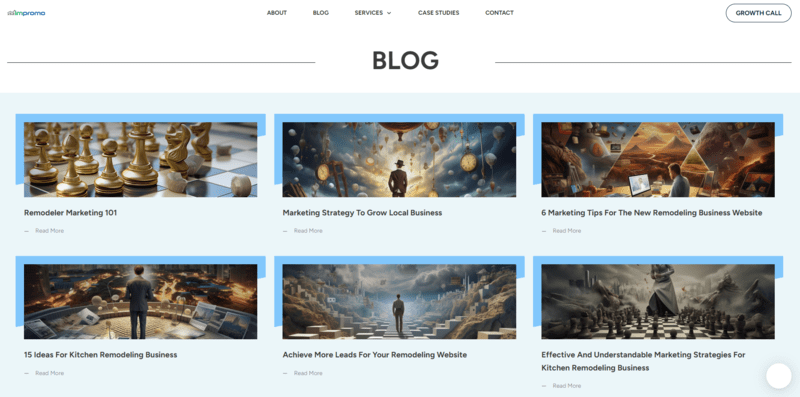
The most important aspect WordPress.com brings from its counterpart, other than its blogging tools, is its plugin library. WordPress.com users have access to over 60,000 free plugins, meaning a WordPress blog can technically have more features than Wix. They won’t all be up to the same quality as Wix, but if you run an affiliate blog or are an influencer who wants to launch a sponsored newsletter, WordPress.com has a much greater selection of email marketing and monetization tools at its disposal.
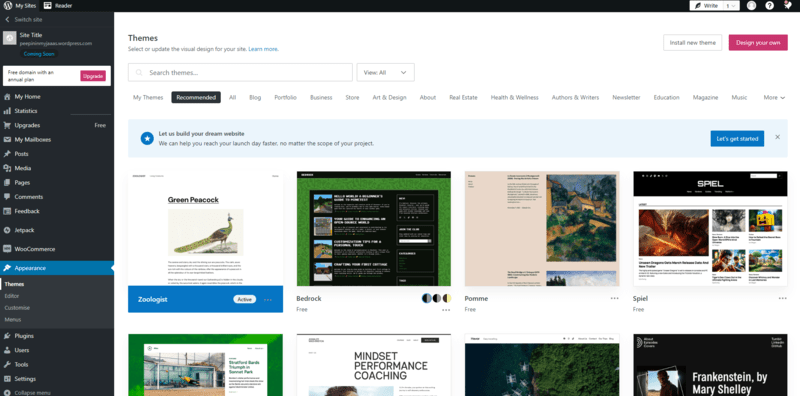
Being built for blogging is reflected in WordPress’ blog themes, which are all meticulously designed. Editing them to exact specifications is still a little bit challenging if you have zero coding knowledge, and we still recommend total beginners stick to Wix and Squarespace for their ease of use.
Additionally, WordPress.com has no in-built SEO tools on either its free or cheapest plan. SEO is vitally important for blogs to be seen and visited by readers, and while you can always use an SEO plugin, it’s still disappointing this feature is locked behind a paywall.
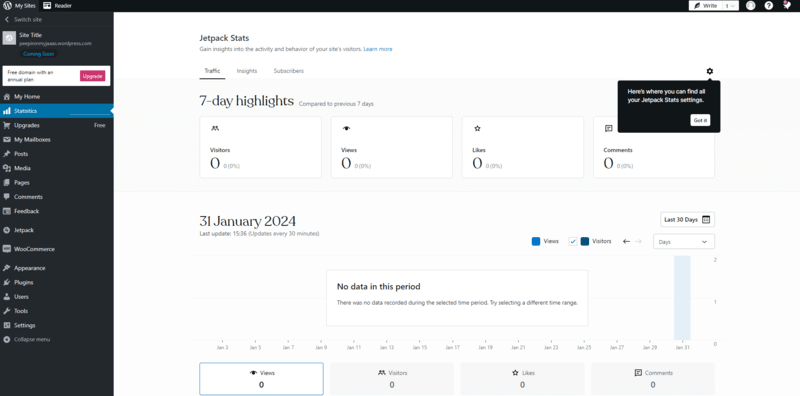
What’s the Best Value Plan?
Here’s a quick look at WordPress.com’s price plans, all billed annually:
- Free plan: $0 per month
- Starter: $4 per month
- Explorer: $8 per month
- Creator: $25 per month
- Entrepreneur: $45 per month
We recommend the Creator plan for all affiliate bloggers wanting to monetize their WordPress blogs because you will need access to both ecommerce and WordPress.com’s plugin library. This will give you access to email marketing features and Google AdSense (getting paid for having ads on your site), plus membership capabilities.
More Information:
- Check out our 15 easy WordPress SEO Tips to learn how to boost your WordPress blog’s SEO.
Best for Entertainment Blogging
Reviews, travel blogs, writing blogs, art blogs, etc.
- Well-designed templates
- Easy-to-use editor
- Advanced SEO settings
- Email marketing capabilities
- Google AdSense
- Minimum storage space – 5GB
- Low starting cost
Top Choice: Squarespace
Starting price: $16 per month
Read our full Squarespace Review
Squarespace
For art blogs
- Beautiful blog designs
- Beginner-friendly builder
- Save 10% with code WBE10
Free trial available
Paid Plans: $16 - $52 / month
Pros
-
Professionally-designed blog templates
-
Tons of creative freedom
-
High-quality blogging features
Cons
-
No free plan
-
Need to upgrade to monetize your blog
-
No autosave when editing
Squarespace is our top choice for entertainment blogs due to its impeccably designed blog templates. Covering a range of industries, you will find one that suits the topic and tone of your blog. If not, Squarespace Blueprint can build you a unique template from scratch – all you need to do is answer a few questions.
In perfect synchronization with its templates is Squarespace’s editor – it’s the easiest we’ve tested! Drag and drop the elements wherever you like, customize them, and even if you have no web design experience, Squarespace’s templates make your choices look professional. We found it difficult to make a bad website with Squarespace!
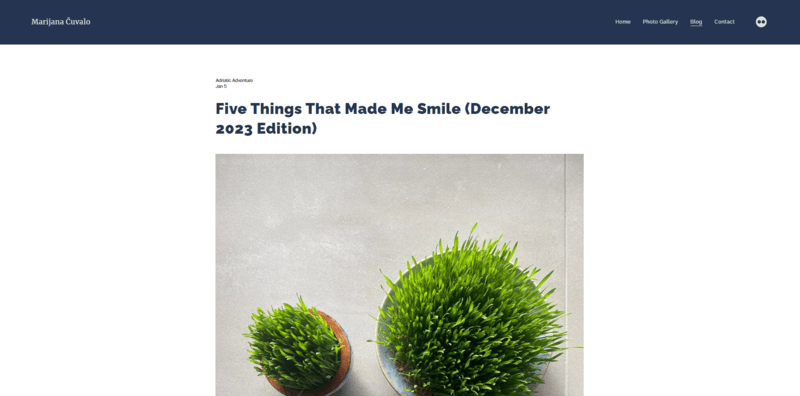
Like Wix, you can add whatever features you would like to your website, but we found Squarespace’s minimalist editor less overwhelming. Squarespace’s blog features are superb, and across all paid plans you get access to comments, RSS feeds, blog analytics, and scheduling. There’s even an AI writer for letting you quickly generate blog posts or ideas, and in our own best AI website builder testing we found it gave you more freedom than Wix’s.
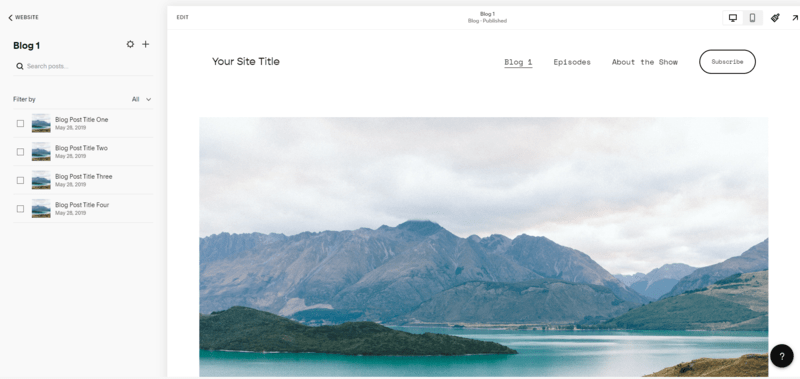
As a blog purely for entertainment, monetization isn’t a requirement, but if you want to you’ll need to upgrade to the Business plan for $23 per month. Squarespace’s SEO tools are also great, giving you SEO settings for individual posts, automatic sitemaps, and Google My Business listing integration. All of this can be managed via Squarespace’s dedicated SEO panel which you can find in the backend.
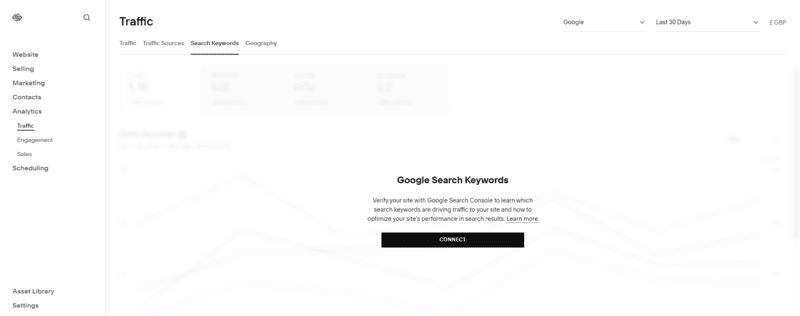
What’s the Best Value Plan?
Here’s a quick look at all of Squarespace’s pricing plans, billed annually:
- Personal: $16 per month
- Business: $23 per month
- Commerce Basic: $28 per month
- Commerce Advanced: $52 per month
Squarespace recently updated its pricing as of April 2024. But, although Squarespace doesn’t come with a free plan, it does start every plan with a 14-day free trial so you can test it out yourself risk-free. For entertainment bloggers, we recommend the Personal plan, because it gives you all the design and blogging tools you need. But if you want to monetize, you’ll need to upgrade to the Business plan – and if you want 10% off at checkout, use our exclusive code WBE.
More Information:
- See who tops our list as the Best Website Builder for Artists.
- See how Squarespace manages in our Wix vs Squarespace article
- We interviewed Marijana Čuvalo about her experience building a blog with Squarespace
Alternative: Hostinger – For simple blogs
Starting price: $2.99 per month + some months free (if you opt for the 48-month plan; promo varies so confirm at checkout)
Read our full Hostinger Review
Hostinger
Best for simple blogs
- A single paid plan
- Best for short-term blogs
- Get online quickly
Paid Plans: $2.99 - $109.99 / month
Pros
-
Drag-and-drop editor
-
Affordable plan
-
Simple to use
Cons
-
Underdeveloped blogging features
-
Lacks advanced SEO tools
-
Limited scalability
Hostinger’s blogging features used to be quite limited. However, since our last round of testing, Hostinger has added features like post scheduling, a search feature, comments, an archive, and analytics to rack your blog’s growth. While its blogging capabilities are strong, it’s weaker in other areas, like SEO, and can feel less developed compared to builders like Wix.
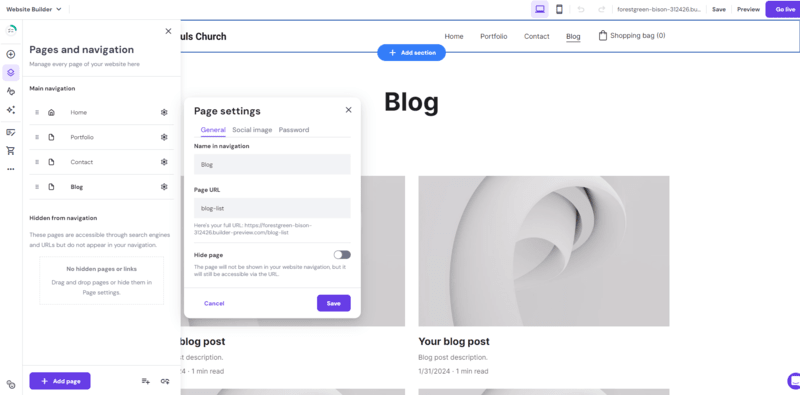
What is it good for then? Well, with its starting plan costing just $2.99 per month (billed annually), Hostinger is perfect for simple blogs. We particularly recommend it for hobby blogs. If you want a blog to post your reviews of music, films, toys, mustard, etc., and have little ambition for scaling it into a full-time career, then Hostinger is the perfect blog website for you.
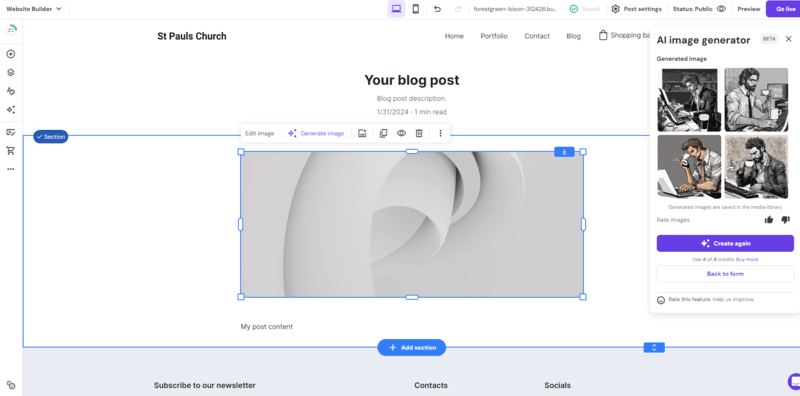
If you are a fan of AI features, then Hostinger may also be the builder for you. Hostinger’s AI Blog Writer can generate written content and images for your blog. This saves a lot of time when coming up with headlines, but we wouldn’t recommend writing your entire blog post with it. Google can tell when you’re using AI and won’t rank it highly in search, plus the AI Imager Generator needs some work – a lot of the images are still a bit…weird.
There is also an AI Logo Maker, an AI Heatmap for seeing which parts of your site get the most attention, and an AI Assistant if you encounter trouble and need some support.
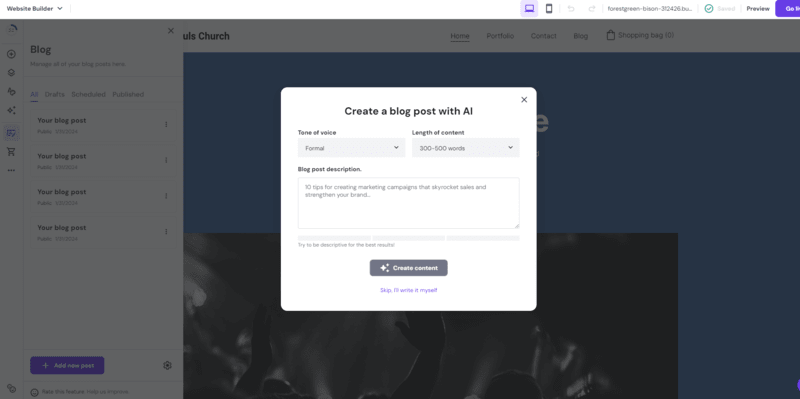
What’s the Best Value Plan?
Hostinger includes its website builder with its hosting plans, but you can also choose one of its dedicated website builder plans:
- Premium Website Builder – $2.99 per month, billed annually
- Business Website Builder – $3.99 per month, billed annually
These prices are for a 12-month plan, although you’ll get the same price if you choose a 24 or 48 subscription too. And if you opt for the 48-month plan, Hostinger often throws in a free month or two as a bonus. Although, this varies so keep an eye out on your checkout page to see what’s available at the time.
If you want a month-by-month plan, it’ll cost you more: $11.99 for the Premium plan and $13.99 for the Business plan.
We recommend the annual $2.99/month Premium plan for all hobby bloggers because the affordable price and simplistic editing will serve your goals better than a feature-loaded and expensive builder like Wix.
More Information:
- Check out our How to Start a Music Blog guide.
Best for Informational Blogging
News blogs, personal finance blogs, sports blogs, science blogs, recipe blogs, etc.
- Well-designed templates
- Post scheduling
- Advanced SEO settings
- Email marketing capabilities
- Google AdSense
- Minimum storage space – 10GB
- Multiple authors
Top Choice: WordPress.org
Starting price: $2.95 per month
Read our full WordPress.org Review
WordPress.org
For news blogs
- Famous for blogging
- Limitless customizations
- Requires separate hosting
Paid Plans: $2.95 - $5.45 / month
Pros
-
60,000+ plugins to customize your blog
-
Build from scratch with total control
-
Add whatever blogging tools you need
Cons
-
Steep learning curve for beginners
-
You manage security, hosting, updates
-
No in-house support team or resources
The most popular platform on the web for blogging, WordPress.org is not like the other website builders on this list. Rather than having a drag-and-drop editor for building a website, WordPress.org instead is a CMS (content management system) and functions entirely around the creation and posting of content. This allows for limitless customization of your blogs – albeit with the caveat that you know how to code HTML.
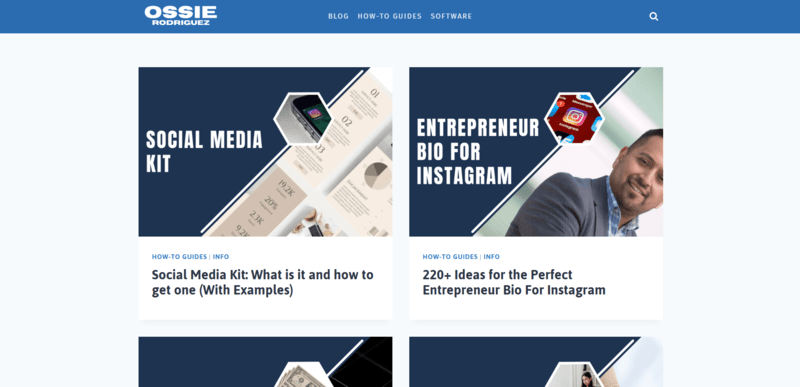
WordPress.org is open-source, meaning that anyone can download and edit it for free. This means your website is endlessly moddable. Everything from design, integrations, marketing, monetization, and storage is all able to be changed by you… as long as you know how. And if you don’t, you’ll need to install extra plugins to make your life easier, such as drag-and-drop plugin Elementor.
Whereas other builders take care of things like hosting and security, you will have to organize that yourself too. WordPress.org itself recommends the web host Bluehost for this and so do we, because of how well it performed in our WordPress hosting research.
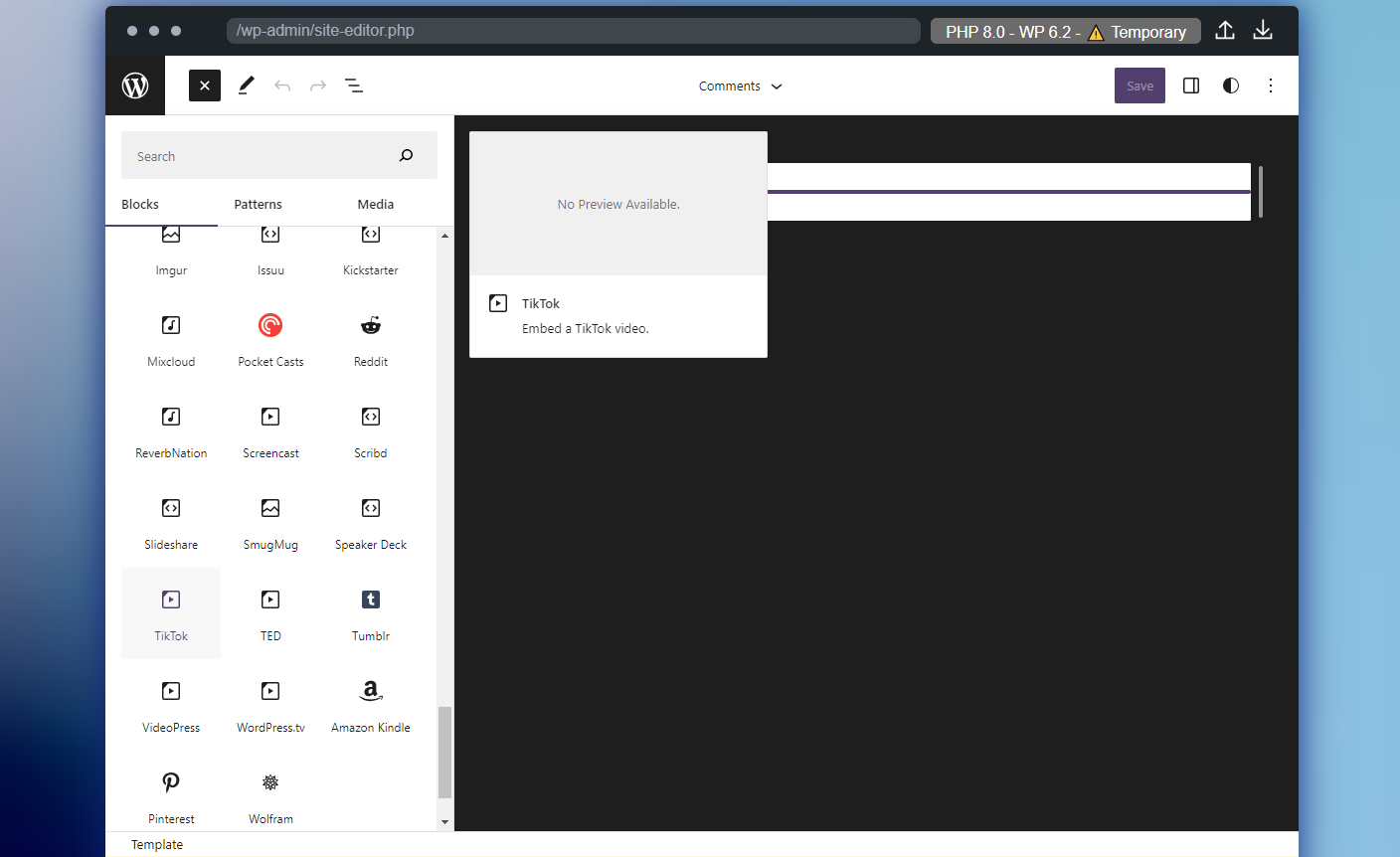
Once you’re over the learning curve, WordPress.org can be rewarding, especially for news and other informational blogs. The content management system lets you grant access to multiple authors to create and schedule hundreds of blog posts at a time and includes everything from forums and comments sections to RSS feeds and analytics.
Better yet, through its plugin library, you can add powerful SEO tools like Yoast and monetize your blog through affiliate marketing programs. While WordPress.org is certainly more work than, say, Wix, it can yield powerful results for bloggers who want to produce lots of informational content with consistent upload schedules.

What’s the Best Value Plan?
Because WordPress.org is free, it doesn’t have traditional pricing plans. However, its recommended hosting provider Bluehost’s pricing plans are as follows:
- Basic: $1.99 per month
- Choice Plus: $3.49 per month
- Online Store: $6.99 per month
- Pro: $8.99 per month
We recommend the Basic plan. Not only is it a fantastic price at only $1.99 per month (billed annually), but you also get 10GB of storage with it. Additionally, Bluehost offers Managed WordPress on the Basic plan, which means Bluehost will take over the management of your site. This is useful support to have, especially as WordPress.org offers no help or support guides itself.
Just be warned that these are introductory prices, and after the initial term, the discounts will be replaced with the standard fee. For example, the Basic plan rises to $3.99 per month following the first year.
More Information:
- Check out our How to Start a WordPress Blog for more tips on getting started.
Alternative: Webflow – For business advice blogs
Starting price: $14 per month
Read our full Webflow Review
Webflow
For business advice blogs
- Advanced customization
- Dependable support
- CMS-powered templates
Free plan available
Paid Plans: $14 / month
Pros
-
No ads on free plan
-
Ideal for experienced builders
-
2,000+ templates
Cons
-
SEO features not available on free plan
-
No drag-and-drop editor
-
Not very easy to use
Webflow is similar to WordPress.org in that code is often required to implement edits and there can be a steep learning curve for beginners. However, while WordPress is a CMS, Webflow is primarily designed for web developers. Webflow’s editor is the most advanced and technical on this list, and if you have web design software skills, you can make professional-looking blogs from scratch. If you’re less experienced, you can simply download a user-made template for free from Webflow’s community marketplace.

While Webflow isn’t a true CMS like WordPress.org, it does have CMS-powered templates. This makes it well-suited for informational blogs, letting you schedule up to 50 CMS items and 50 form submissions even on its free plan. Combining this with its advanced design tools and editor, Webflow is great for online business blogs, as you can show your expertise through both the quality of your written content and your site’s design – if you know how.
Zero web design or coding knowledge may hold you back with Webflow, and you might be more suited to Wix or Squarespace’s more accessible editors.
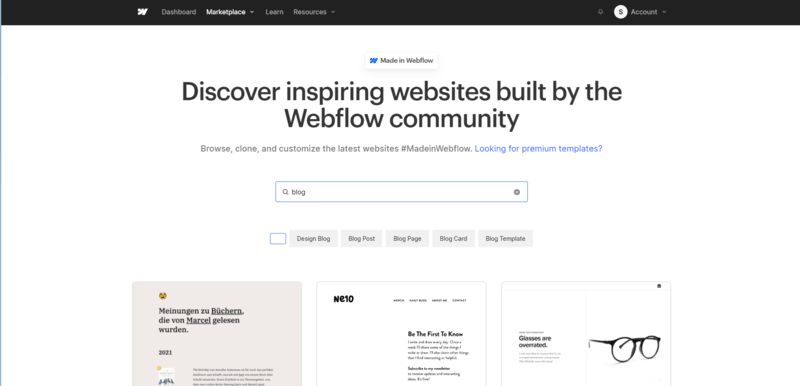
Webflow has a free plan, but this doesn’t provide CMS blogging features or any SEO tools, meaning you will need to upgrade. Compared to Wix, these SEO tools aren’t as good as you do not get access to personalized SEO tips or SEO settings for every blog post.
Unlike WordPress, there is no plugin library to make up for this lack of features. This also affects what monetization you can have with Webflow, though you will still have access to Google AdSense (through code) and ecommerce (if you choose an ecommerce plan).
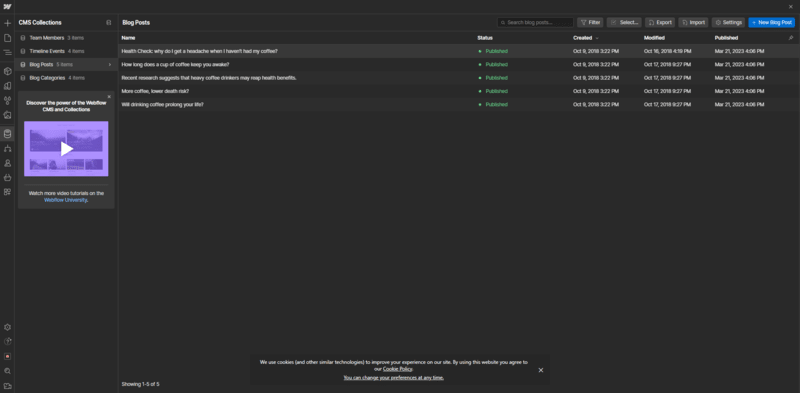
What’s the Best Value Plan?
Here’s a look at Webflow’s price plans (billed annually):
- Free: $0 per month
- Basic: $14 per month
- CMS: $23 per month
- Business: $39 per month
For blogging, we’d recommend the CMS plan. The free plan and Basic plan don’t come with CMS functions, making them pretty useless for blogging. The CMS plan gives you 200GB of storage, 2,000 CMS items, site search, and user accounts for three content editors.
More Information:
- See which of these website builders wins the battle of design in our Squarespace vs Webflow head-to-head
How To Choose Your Blog’s Website Builder
We ask and interview professional bloggers for their take when crafting our methodology. We work out what real bloggers love about their platforms and what they wish they had. The needs for your blog are going to massively differ depending on the content, style, and direction you want to take it in, but through our own experiences – and those of other bloggers – we’ve narrowed it down to four questions you need to ask yourself before buying:
- Is the website builder suitable for my blog style?
- Can I build my blog how I want to?
- Can I grow the audience for my blog?
- Can I monetize my blog?
Not all website builders will be the right fit. For example, using Wix for a personal hobby blog would be fine, but you may be better off with the more affordable Hostinger. Likewise, if you plan to monetize and grow your blog into a proper business, you’re going to want a more scalable website builder like Wix or Squarespace.
How We Test
In addition to the blogging-focused research and website builder analysis, we also carried out hands-on testing so we could share our experiences with the platforms when writing our reviews. But it wouldn’t be fair if we, as experts, were the only ones testing each platform. So, we got everyday people to use each builder and share their feedback with us – all so you can make the best choice possible when choosing your blog’s website builder.
To bring you a list of the best blogging platforms, we used our rigorous research methodology and our own hands-on experience to weed out the poor performers and showcase the best options. We want to make sure that you are choosing the right blogging platform, so we changed the weighting of our scores to categories that are relevant to bloggers, like blogging features, SEO, and storage – plus important tools such as analytics and archives. We’ve also rolled less important categories like value for money, ease of use, and help and support into one singular score.
You can rest easy knowing the score we gave only reflects the best of the best when it comes to blogging and blogging alone. Here are the unique weightings of our blogging category:
- Blogging – 50%
- Website Features – 35%
- SEO – 10%
- Overall score – 5%
The 6 Best Blogging Platforms: Summary
There you have it – our list of the best blogging platforms! Based on hours of research, Wix is our top choice for blogging. It’s a great overall builder, offering tons of built-in blog features and powerful SEO tools to help you promote your content online.
Ready to start your blog? If so, check out our guide on How to Write a Blog Post.
Till then, happy blogging!
31 comments